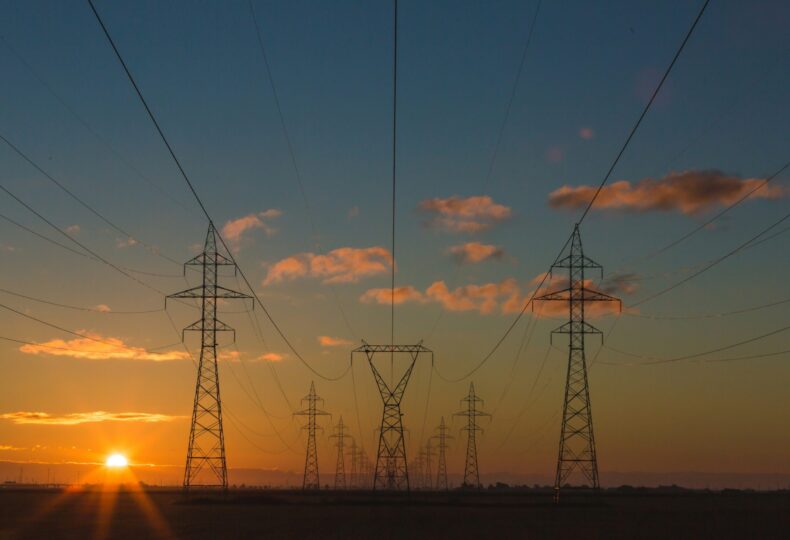
工場の省エネとは?投資回収期間や補助金活用から具体的な削減事例まで徹底解説
工場の省エネ対策は、年々上昇するエネルギーコストへの対応や企業の持続可能な成長に不可欠な取り組みです。本記事では、省エネ法における工場の位置づけから、具体的な設備投資の方法、運用改善のポイント、さらには補助金の活用方法まで、工場における効果的な省エネ対策について、成功事例を交えながら詳しく解説します。
目次
1. 工場の省エネ対策の基礎知識
工場の省エネ対策は、企業の持続可能な成長と競争力強化に不可欠な取り組みとなっています。近年のエネルギーコストの上昇により、事業者の経営を圧迫する要因となっているため、効果的な省エネ対策の実施が急務となっています。
1.1. 省エネ法における工場の位置づけ
省エネ法では、一定以上のエネルギー使用量がある工場は特定事業者として指定され、様々な義務が課せられています。具体的には、年間エネルギー使用量が原油換算で1,500kl以上の事業者は、エネルギー管理指定工場として定期報告書の提出や中長期計画の策定が求められています。この法規制への対応は、工場の省エネ対策を推進する上で重要な基盤となっています。
1.2. エネルギー使用量の現状分析
工場のエネルギー使用量を把握することは、効果的な省エネ対策を実施する第一歩です。消費電力量の測定や、設備ごとの使用量を詳細に分析することで、省エネ効果が高い領域を特定できます。資源エネルギー庁の調査によると、多くの工場では生産設備や空調設備でのエネルギー消費が大きな割合を占めていることが明らかになっています。
1.3. 工場のエネルギーコスト構造
工場における電気料金や燃料費などのエネルギーコストは、事業全体の収益性に大きな影響を与えます。特に製造業において、エネルギーコストの削減は直接的な利益改善につながります。エネルギー使用量を可視化し、コスト構造を正確に把握することで、効果的な省エネ対策の立案が可能となります。
1.4. 省エネ対策による具体的な削減効果
適切な省エネ対策を実施することで、大きな削減効果が得られます。例えば、高効率な設備への更新や運用改善により、10-30%程度のエネルギーコスト削減が実現できるケースも少なくありません。
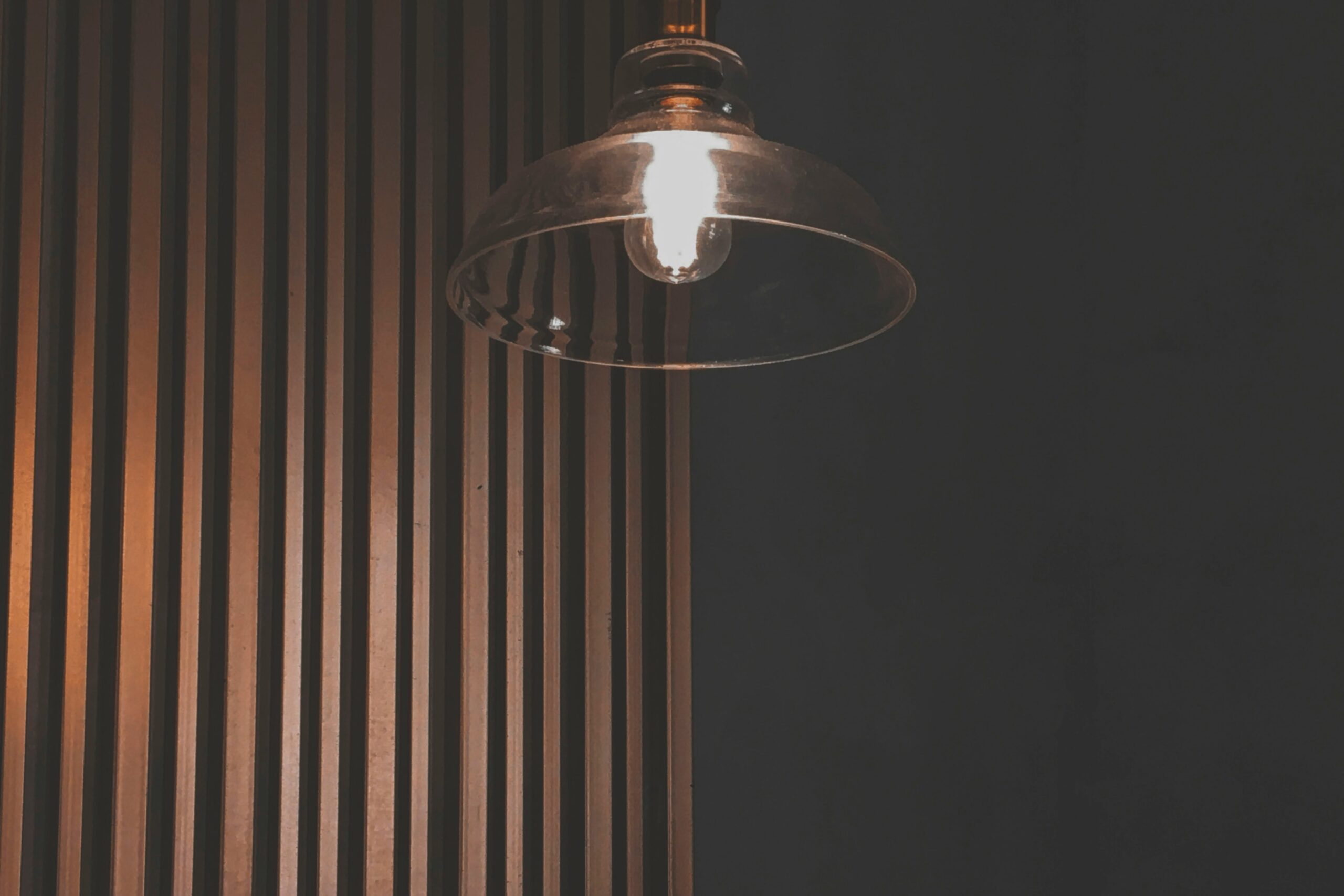
2. 具体的な省エネ施策と導入効果
工場の省エネ対策は、設備の更新から運用改善まで多岐にわたります。それぞれの対策について、具体的な導入方法と期待される効果を解説します。
2.1. 生産設備の省エネ化
生産設備の省エネ化は、工場の省エネ対策の中核を担います。インバータ制御の導入や高効率モーターへの更新により、消費電力量を大幅に削減できます。定期的なメンテナンスを実施することで、設備の効率低下を防ぎ、安定した省エネ効果を維持することが可能です。
2.2. 工業炉の高効率化対策
工業炉の省エネ対策として、リジェネレイティブバーナーの導入が注目されています。従来型のバーナーと比較して、熱エネルギーの利用効率が大幅に向上し、燃料費の削減に大きく貢献します。また、断熱性能の強化や運転条件の最適化により、さらなる省エネ効果が期待できます。
2.3. LED照明の導入とコスト削減効果
照明のLED化は、比較的導入が容易で効果が明確な省エネ対策です。従来の蛍光灯や水銀灯と比較して、LED照明の導入により50-80%の消費電力削減が可能です。さらに、長寿命化によるメンテナンスコストの削減も実現できます。
2.4. コンプレッサー設備の最適化
工場の電力使用量の中で大きな割合を占めるコンプレッサー設備の最適化は、重要な省エネ対策となります。エアー漏れの定期点検や、インバータ制御の導入により、電力量を15-30%程度削減できることが実証されています。
2.5. 空調システムの効率改善
空調システムの効率改善は、年間を通じて大きな省エネ効果が得られます。温度設定の適正化や、高効率機器への更新、外気導入量の最適化などにより、エネルギー使用量の削減を実現できます。
2.6. 熱エネルギーの回収と再利用
工場では様々な工程で熱が発生しており、この排熱を効果的に回収・再利用することで、大きな省エネ効果が得られます。熱交換器の設置や、コジェネレーションシステムの導入により、エネルギーの有効活用が可能となります。実績のある工場では、熱エネルギーの再利用により、年間のエネルギーコストを20%以上削減した事例も報告されています。
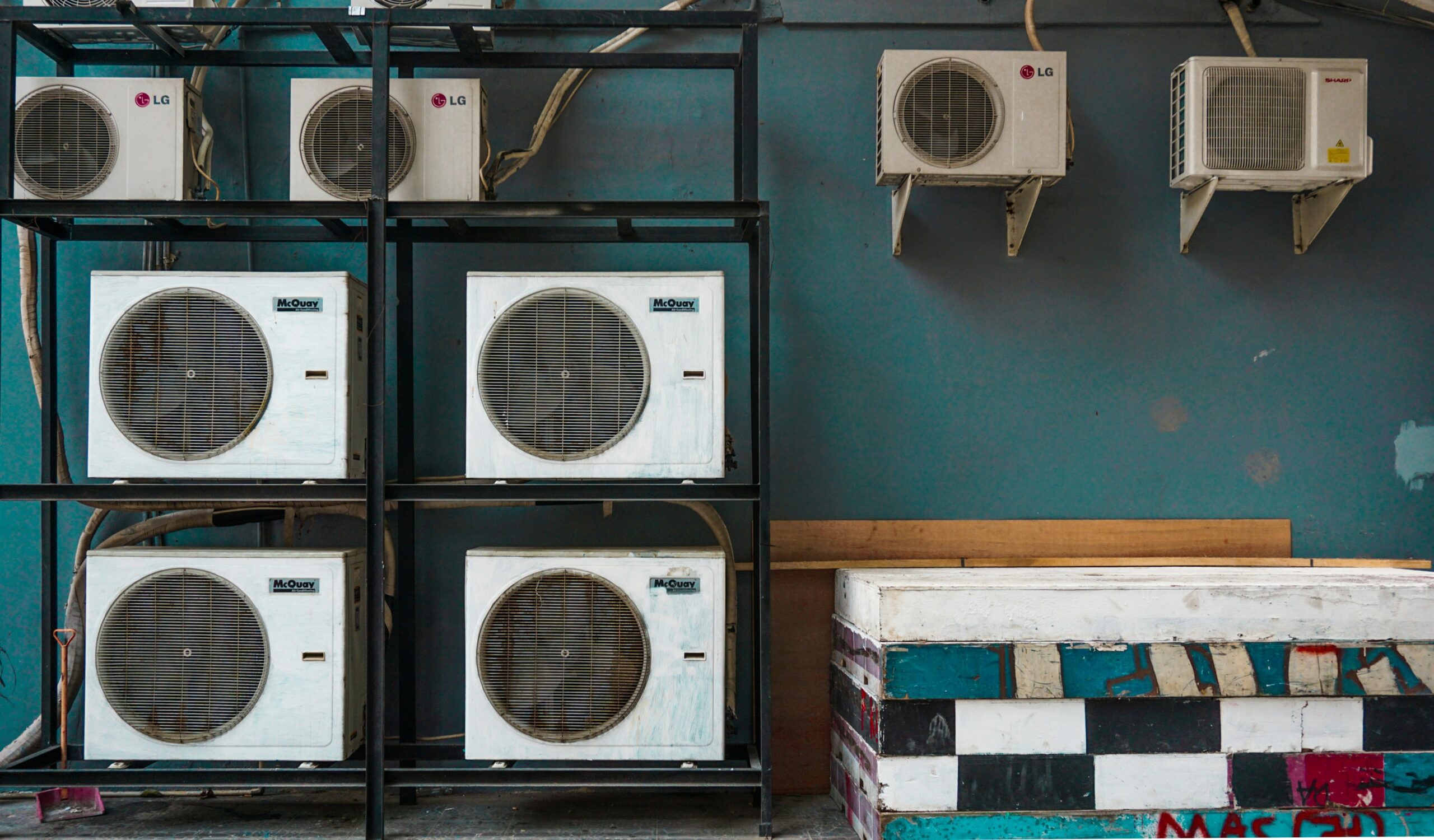
3. 省エネ設備投資の実践ガイド
工場の省エネ対策を効果的に進めるためには、計画的な設備投資が不可欠です。投資効果を最大化するためには、現状分析から実施後の効果測定まで、体系的なアプローチが必要となります。
3.1. 設備更新計画の立て方
省エネ設備への更新は、工場の消費電力量やエネルギーコストに大きな影響を与えます。設備の導入工場における実績データを参考に、優先順位をつけて計画を立てることが重要です。特に、エネルギー使用量が多い設備から順次更新を進めることで、投資効果を最大化できます。
3.2. 投資対効果の算出方法
省エネ対策の投資判断には、具体的な数値に基づく効果予測が必要です。投資額に対する省エネ効果を算出し、投資回収期間を明確にすることで、経営判断の基準とすることができます。削減効果は、エネルギーコストの削減額だけでなく、CO2削減ポテンシャルも考慮に入れる必要があります。
3.3. 補助金・助成金の活用術
省エネ設備の導入には、様々な補助金や助成金制度を活用できます。資源エネルギー庁が提供する支援制度を活用することで、初期投資の負担を軽減できます。特に中小企業の事業者向けには、手厚い支援制度が用意されています。
3.4. リジェネレイティブバーナーの導入事例
工業炉の省エネ対策として、リジェネレイティブバーナーの導入が注目されています。この技術により、熱エネルギーの効率的な利用が可能となり、燃料費の大幅な削減が実現できます。導入企業の実績では、30%以上の省エネ効果が得られています。
4. 運用改善による省エネ対策
設備投資だけでなく、日常的な運用改善も重要な省エネ対策となります。効果的な運用改善には、組織的な取り組みと継続的なモニタリングが不可欠です。
4.1. エネルギー管理体制の構築
工場の省エネを推進するには、確実なエネルギー管理体制の構築が必要です。エネルギー使用量を定期的に計測し、データに基づいた改善活動を展開することで、持続的な省エネ効果が得られます。
4.2. 消費電力量の見える化
消費電力量の見える化は、効果的な省エネ対策の基盤となります。設備ごとの電力使用量を把握し、ムダの発見や改善効果の確認に活用します。IoTセンサーやエネルギー管理システムの導入により、リアルタイムでの監視が可能となります。
4.3. 定期的なメンテナンス計画
設備の定期的なメンテナンスは、省エネ効果を維持するために重要です。特に生産設備や工業炉の効率低下を防ぐため、計画的な点検と整備が必要となります。メンテナンス計画を適切に実施することで、安定した省エネ効果が得られます。
4.4. 従業員の意識改革と教育
省エネ対策の成功には、従業員の協力が不可欠です。定期的な教育訓練を実施し、省エネの重要性や具体的な取り組み方法について理解を深めることで、全社的な省エネ活動が推進できます。
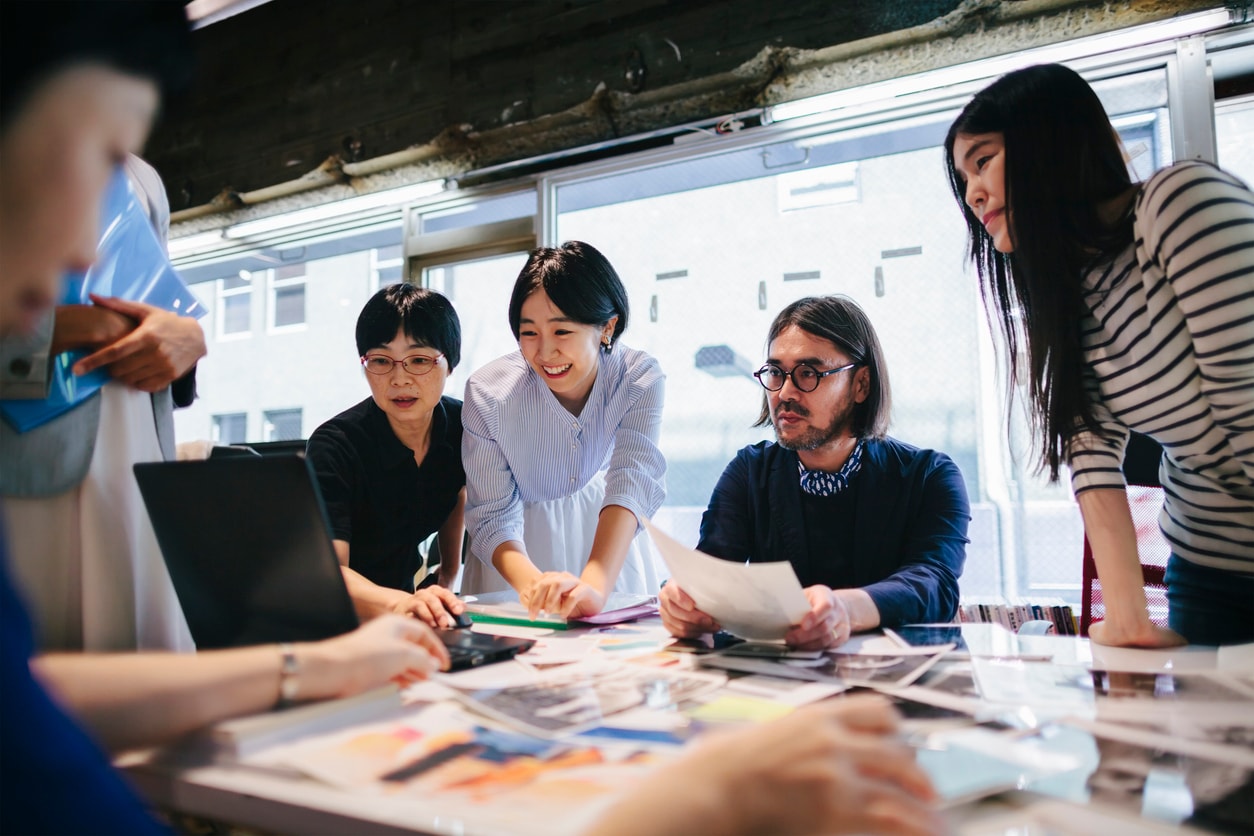
5. 先進的な省エネ技術の導入
最新のテクノロジーを活用した省エネ対策は、さらなる効率化を実現する可能性を秘めています。デジタル技術の活用により、きめ細かな制御と最適化が可能となります。
5.1. IoT活用による電力の最適化
IoT技術を活用することで、工場の電力使用量をリアルタイムで把握し、効率的な運用が可能となります。各設備の稼働状況に応じて、最適な電力供給を実現することで、大きな省エネ効果が得られます。
5.2. AI制御システムの実装
AI技術を活用した制御システムにより、生産設備の運転条件を最適化することができます。過去のデータを分析し、最適な運転パターンを自動的に選択することで、エネルギー使用量の削減を実現します。
5.3. 再エネ設備の統合
工場の省エネ対策として、再エネ設備の導入も重要な選択肢となっています。太陽光発電システムなどの再エネ設備を導入することで、電力コストの削減と環境負荷の低減を同時に実現できます。
5.4. 次世代省エネ技術の展望
省エネ技術は日々進化しており、新たな可能性が広がっています。例えば、蓄電システムとの連携や、デジタルツインを活用した設備運用の最適化など、革新的な技術の実用化が進んでいます。これらの技術を積極的に導入することで、さらなる省エネ効果が期待できます。
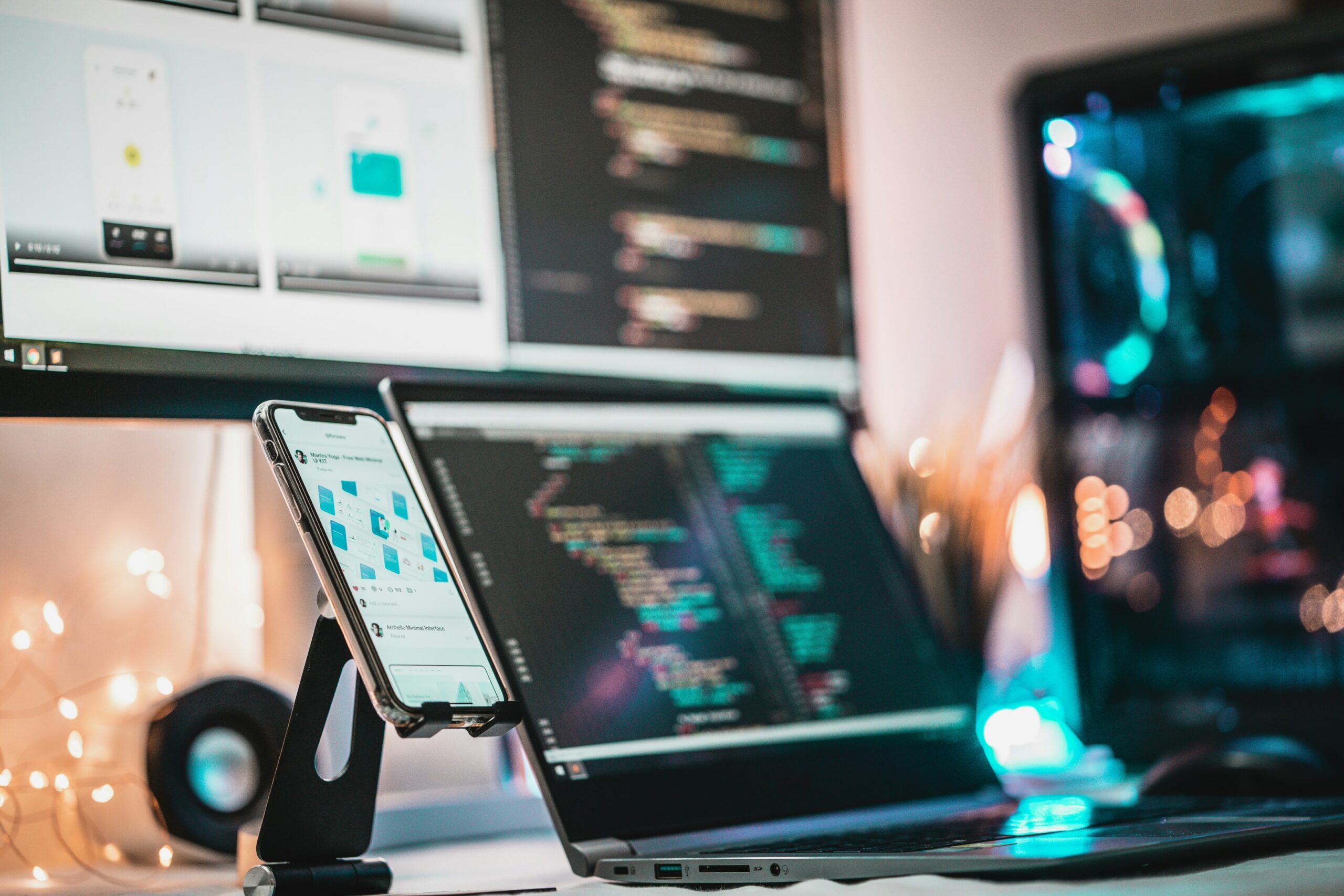
6. 成功企業の省エネ事例研究
工場の省エネ対策において、先進的な取り組みを行っている企業の事例は、具体的な実施方法や期待される効果を理解する上で重要な参考となります。ここでは、様々な規模の企業における成功事例を紹介します。
6.1. 大手製造業の取り組み実績
大手製造業では、包括的な省エネ対策により大きな成果を上げています。例えば、エネルギー管理システムの導入と設備の高効率化により、工場のエネルギー使用量を年間15%削減した事例や、生産設備の運用改善により電気料金を20%削減した実績があります。これらの企業では、省エネ効果の持続的な向上を実現しています。
6.2. 中小企業の省エネ成功例
中小企業の事業者においても、効果的な省エネ対策を実施している事例が増えています。特に、LED照明の導入や空調設備の最適化など、投資対効果の高い施策から段階的に実施することで、着実な省エネ効果を実現しています。補助金を活用した設備更新により、初期投資の負担を抑えながら省エネを推進している例も多く見られます。
6.3. CO2削減ポテンシャルの実現方法
工場におけるCO2削減ポテンシャルを最大限に引き出すためには、複合的なアプローチが必要です。省エネ設備の導入に加え、再エネの活用や熱エネルギーの効率的な利用により、地球温暖化対策としての効果を高めることができます。実際の導入工場では、年間30%以上のCO2排出削減を達成した事例も報告されています。
6.4. 市場競争力向上の実証データ
省エネ対策の実施により、企業の市場競争力が向上することが実証されています。エネルギーコストの削減による収益性の改善に加え、環境配慮型企業としてのブランド価値向上にもつながっています。特に、省エネ法への対応を積極的に進めている企業では、持続可能な成長を実現しています。
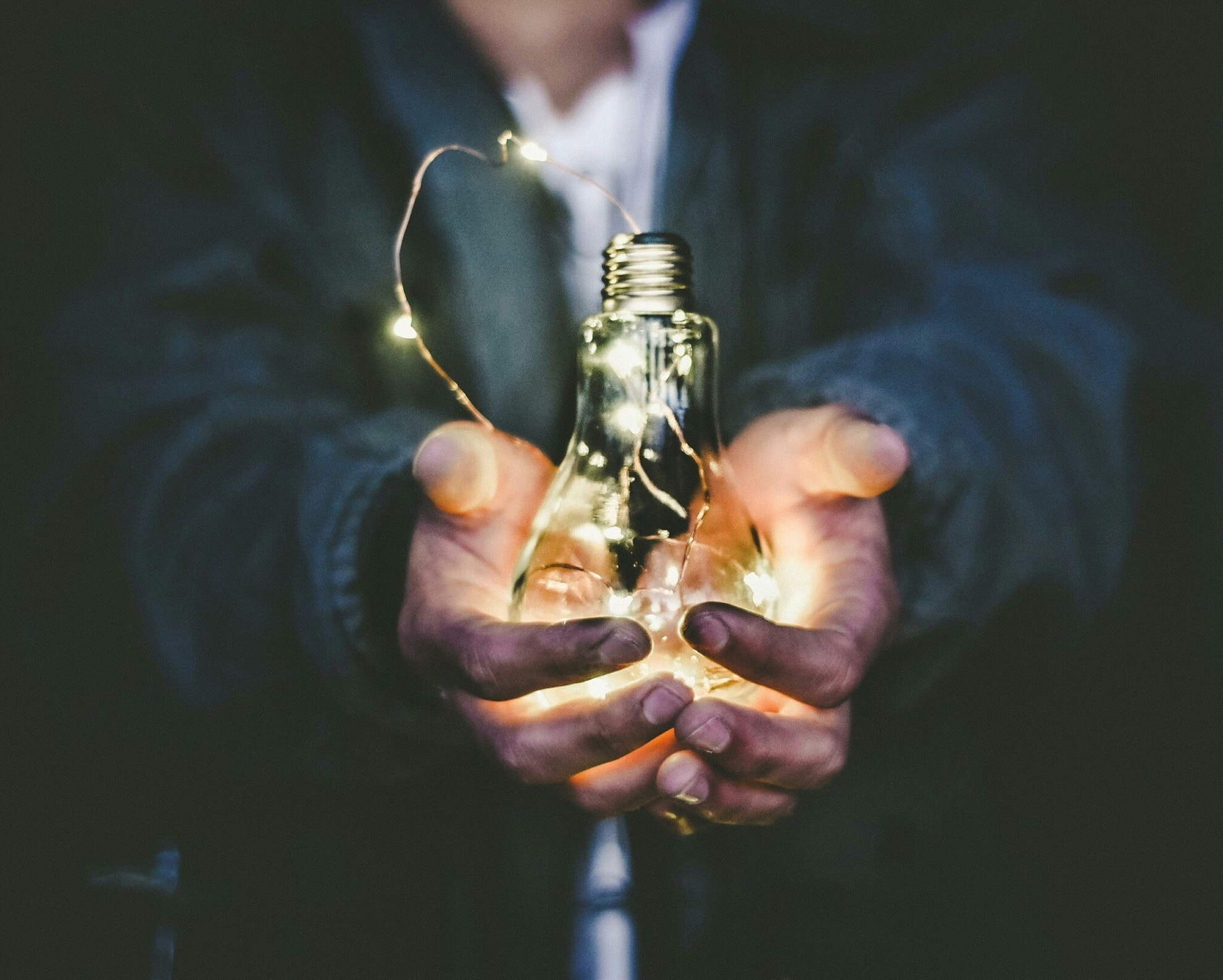
7. 法規制対応と報告実務
省エネ対策を進める上で、関連法規制への適切な対応は不可欠です。ここでは、事業者が遵守すべき主要な要件と実務的なポイントを解説します。
7.1. 定期報告書の作成方法
省エネ法に基づく定期報告書の作成には、正確なエネルギー使用量の把握と適切な記録管理が必要です。特に、エネルギー管理指定工場では、消費電力量や燃料使用量などの詳細なデータ収集が求められます。報告書作成の効率化のため、エネルギー管理システムを活用している事例も増えています。
7.2. エネルギー管理指定工場の義務
エネルギー管理指定工場には、省エネ法に基づく様々な義務が課せられています。エネルギー管理者の選任や中長期計画の策定など、具体的な対応が必要となります。これらの義務を確実に履行することで、効果的な省エネ推進体制を構築できます。
7.3. 地球温暖化対策の要件整理
工場における地球温暖化対策は、国や地方自治体の規制に基づいて進める必要があります。CO2削減目標の設定や排出量の報告など、具体的な要件を理解し、計画的な対応を進めることが重要です。資源エネルギー庁のガイドラインに沿った取り組みを実施することで、確実な対応が可能となります。
7.4. 事業者クラス分け評価制度
省エネ法に基づく事業者クラス分け評価制度では、企業の省エネ取り組み状況が評価されます。優良事業者として評価されることで、企業イメージの向上や競争力の強化につながります。評価基準を理解し、計画的な改善を進めることが重要です。
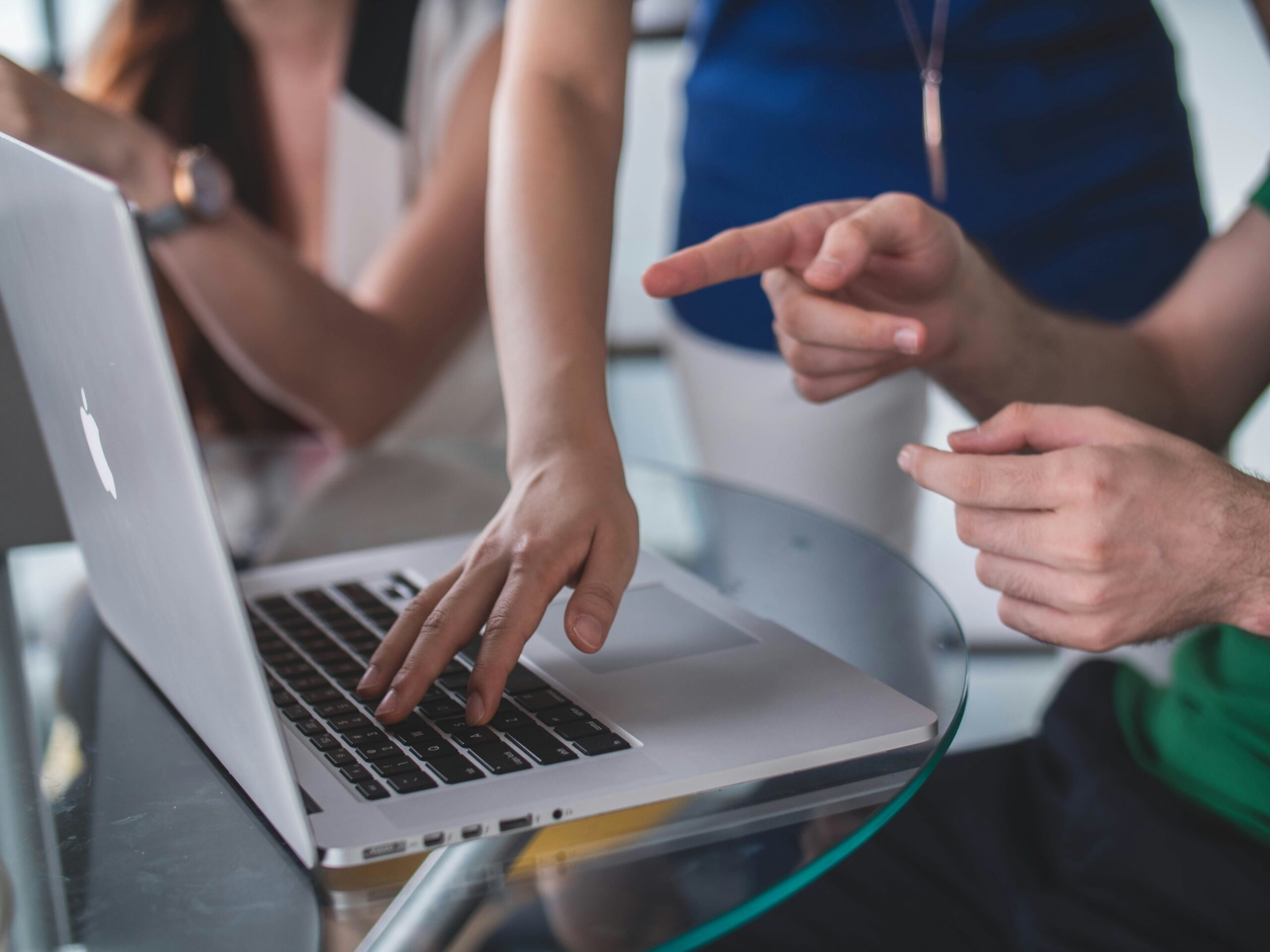
8. 今後の展望と対策ロードマップ
工場の省エネ対策は、技術革新やエネルギー政策の変化に応じて進化を続けています。将来を見据えた戦略的な取り組みが求められています。
8.1. 2030年に向けた削減目標
2030年に向けて、より高い省エネ目標が設定されています。工場のエネルギー使用量を効果的に削減するため、中長期的な視点での設備投資計画や運用改善が必要となります。特に、CO2削減ポテンシャルを最大限に引き出すための戦略的なアプローチが求められています。
8.2. 省エネ技術の発展予測
IoTやAIなどのデジタル技術の進化により、さらなる省エネ効果が期待されています。次世代の省エネ技術の動向を把握し、適切なタイミングでの導入を検討することが重要です。特に、再エネとの連携や革新的な制御技術の活用が注目されています。
8.3. 事業全体の最適化戦略
工場の省エネ対策は、個別の施策だけでなく、事業全体の最適化という視点で考える必要があります。生産効率の向上や品質管理との連携など、総合的なアプローチによる価値創造が求められています。
8.4. 持続可能な工場運営の実現
持続可能な工場運営の実現に向けて、省エネ対策は重要な役割を果たします。環境負荷の低減と経済性の両立を目指し、長期的な視点での取り組みを進めることが必要です。エネルギーコストの削減と市場競争力の向上を同時に実現することで、企業の持続的な成長が可能となります。
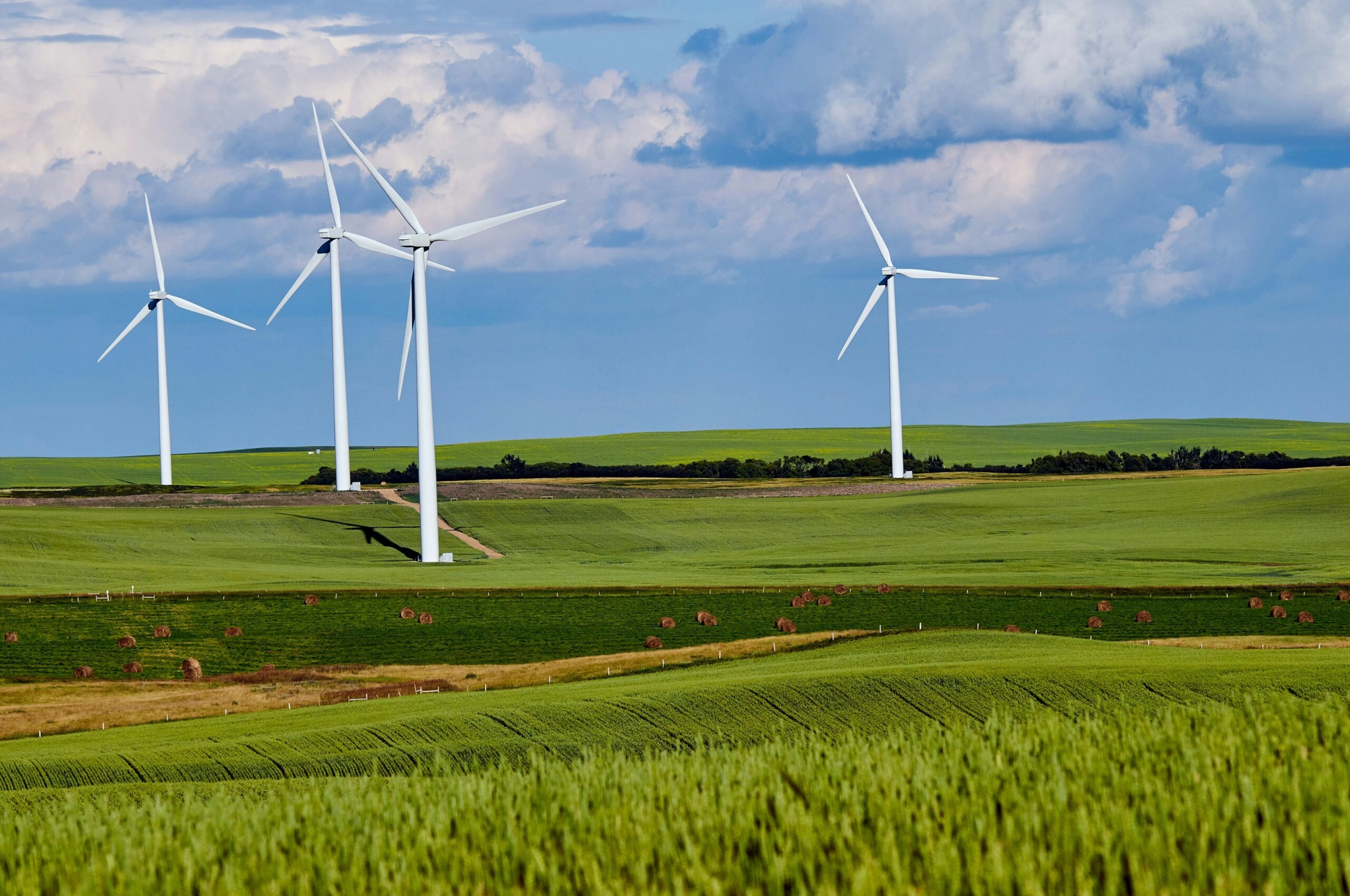
よくある質問と回答
工場の省エネ対策は具体的に何から始めればよいですか?
工場の省エネ対策は、まずエネルギー使用量の現状把握から始めることをお勧めします。消費電力量を計測し、どの設備で多くのエネルギーが使用されているかを分析します。その上で、LED照明への更新や空調設備の最適化など、投資対効果の高い施策から順次実施していくことが効果的です。
省エネ対策の費用対効果はどの程度ですか?
省エネ対策の費用対効果は、施策の内容により異なりますが、多くの場合、数年で投資回収が可能です。例えば、LED照明の導入では2-3年、高効率な生産設備への更新では3-5年程度で投資回収できるケースが多く報告されています。また、補助金を活用することで、さらに投資回収期間を短縮できます。
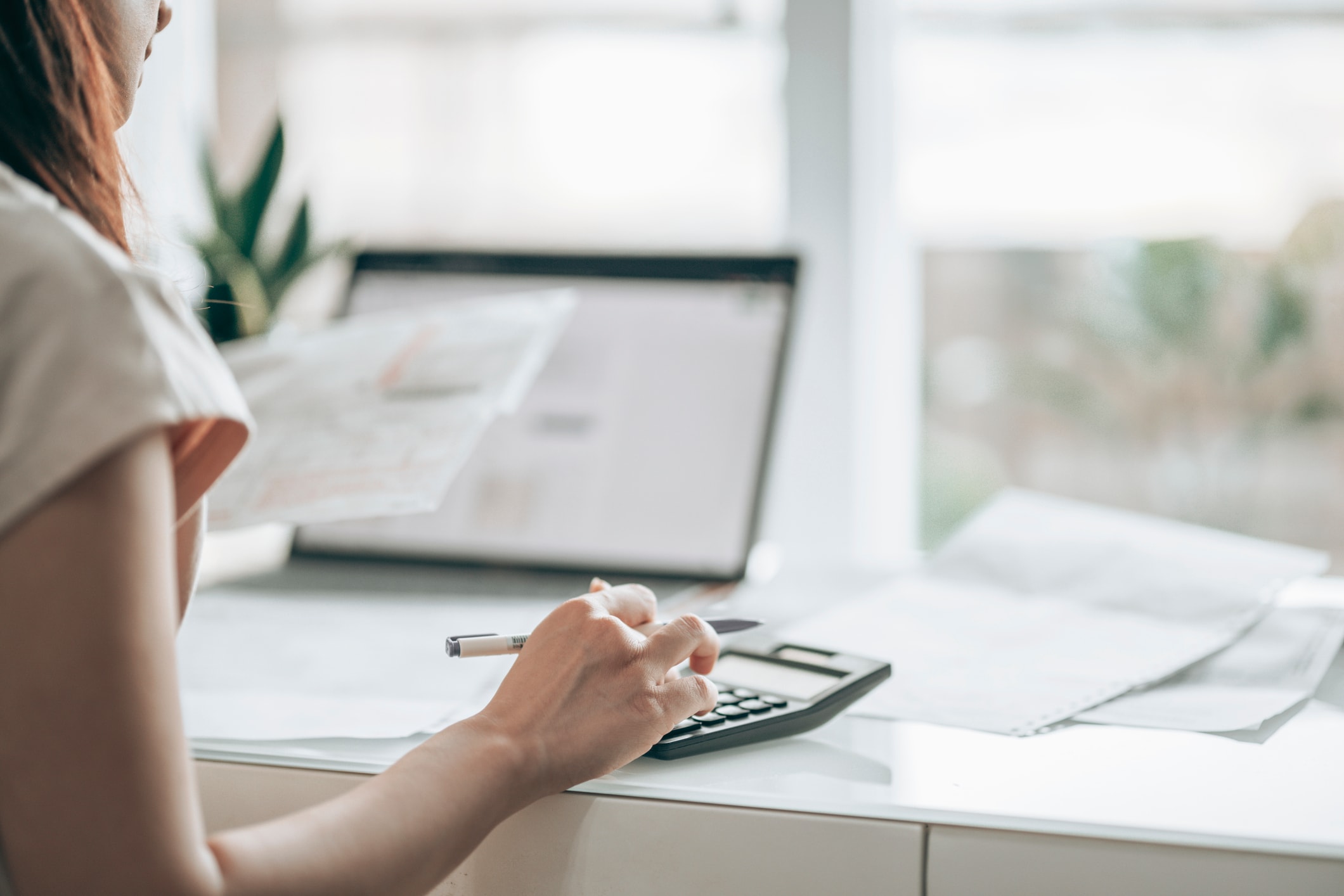
省エネ法の対象となる工場の基準は何ですか?
省エネ法では、年間のエネルギー使用量が原油換算で1,500kl以上の事業者が、エネルギー管理指定工場として指定されます。該当する工場は、エネルギー管理者の選任や定期報告書の提出などが義務付けられています。
省エネ効果を高めるための運用面での工夫はありますか?
運用面での工夫として、定期的なメンテナンス計画の実施、エネルギー使用量の見える化、従業員教育の徹底などが効果的です。特に、設備の適切な保守管理や運転条件の最適化により、追加投資なしで5-10%程度の省エネ効果が得られるケースもあります。
省エネ対策に使える補助金制度にはどのようなものがありますか?
省エネ設備への更新や省エネ診断に対する補助金制度が、国や地方自治体により提供されています。資源エネルギー庁が実施する「省エネ設備導入補助金」や「省エネ診断事業」などが代表的です。申請時期や要件を確認し、計画的に活用することをお勧めします。
工場の省エネ対策はCO2削減にどの程度効果がありますか?
工場の省エネ対策は、企業のCO2削減目標達成に大きく貢献します。一般的に、高効率設備への更新や運用改善により、工場全体のCO2排出量を10〜30%削減することが可能です。例えば、ボイラの最新型への更新では約15%、コンプレッサーの適正化では約10%のCO2削減が見込めます。また、工場全体のエネルギー管理システム導入により、エネルギー使用量の推移を可視化し、継続的な改善につなげることで、さらなる削減効果が期待できます。
工場の脱炭素化に向けた中長期的な取り組みには何がありますか?
工場の脱炭素化に向けた中長期的な取り組みとしては、省エネ設備の段階的更新に加え、再生可能エネルギーの導入が重要です。特に屋根を活用した太陽光発電システムの設置や、工場排熱の有効利用などが効果的です。また、生産プロセスの根本的な見直しによるエネルギー消費量を削減する取り組みも必要です。これらの施策を計画的に実施することで、2030年までに排出量の削減目標達成に貢献し、2050年のカーボンニュートラルに向けた基盤を構築できます。
ボイラの省エネ改善で期待できる効果はどの程度ですか?
ボイラの省エネ改善では、適切な運用管理や設備更新により、燃料消費量を削減し、大きな省エネ効果が期待できます。具体的には、ボイラの運転条件最適化で5〜10%、空気比調整で3〜7%、排熱回収システム導入で10〜15%程度の削減が可能です。特に古いボイラを最新の高効率タイプに更新すると、燃料消費量の15〜25%削減に加え、排出量の削減も実現します。投資回収期間は一般的に3〜5年程度ですが、大型ボイラほど省エネ効果が高く、投資回収が早くなる傾向があります。
工場のエネルギー使用量の推移をどのように分析すればよいですか?
工場のエネルギー使用量の推移を効果的に分析するには、まず設備ごとの電力計測システムを導入し、時間帯別・工程別のデータ収集が重要です。収集したデータは、生産量あたりのエネルギー原単位として整理し、月次や季節ごとの変動パターンを把握します。また、他の工場や業界平均値とのベンチマークを行うことで、改善余地を特定できます。これらの分析結果をもとに、省エネに向けた具体的な対策を立案し、実施後も定期的にデータを確認して効果検証を行うことが成功の鍵となります。
工場の排出量の削減に効果的な設備投資の優先順位は?
工場の排出量の削減に効果的な設備投資の優先順位は、まず投資回収期間が短く、CO2削減効果が大きい施策から着手することが基本です。具体的には、①照明のLED化(投資回収2〜3年)、②コンプレッサーやポンプのインバーター化(2〜4年)、③高効率モーターへの更新(3〜5年)、④ボイラの高効率化(3〜6年)、⑤生産設備の更新(5〜8年)の順が一般的です。また、各工場の特性に合わせた省エネ診断を実施し、エネルギー使用状況に応じた最適な投資計画を策定することが重要です。